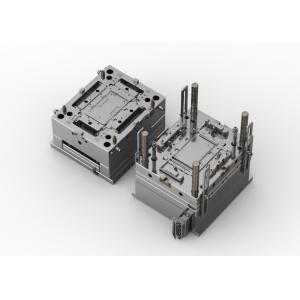
Add to Cart
Transparent Tablet Battery Cover (1*1)
No.23605-B
Description:
Hot Runner Injection Molding is a manufacturing process employed by our company to produce high-quality plastic parts. It involves injecting molten plastic into a mold through a heated channel system, known as the hot runner system. This system ensures continuous plastic molten state during injection, eliminating runners and reducing material waste. Hot Runner Injection Molding offers several advantages. Firstly, it enables faster cycle times by directly injecting molten plastic into the mold without cooling runners. This enhances productivity and reduces lead times. Additionally, eliminating runners reduces material costs and minimizes environmental impact. Our company utilizes advanced hot runner technology for precise control over the injection process. Equipped with temperature sensors and controllers, the hot runner system enables accurate temperature regulation and consistent part quality. This technology also facilitates the production of complex parts with tight tolerances. Hot Runner Injection Molding finds extensive application in industries such as automotive, electronics, and consumer goods. It is particularly suitable for large-scale production runs and projects that demand high precision and efficiency. |
Application:
Flat case
Daily necessities
lamps
Mechanical components
Computer Accessories
mobile phone accessories
auto parts
Features:
Brand | Chitwing |
Origin | Guangdong, China |
Mold Base | Customized |
Gate | Pin point gate + side gate |
Type | Three-plates mold |
Tool Life | 500,000 shots |
Standard | LKM |
Cavity & Core Steel | Hardened (1*1/S136) |
Injection/Runner Type | Hot runner |
Surface Finish | Outer surface polished to 800# sandpaper, inner surface EDM with VDI21#, and surface hardened to a minimum of 600HV |
Mold Size | 450 x 500 x 566mm (net weight 600kg) |
Part Size | 212.45 x 124.68 x 7.58mm (net weight 12g) |
The mold is equipped with a 2x hot runner valve gate system that can be converted to cold runner pin point gates. It also features 4 slides and 27 lifters, ensuring exceptional strength, smooth molding, short cycle time, and no material loss from the runner. |
Advantage:
Our company specializes in manufacturing hot runner injection molding molds, which offer a range of significant benefits. Firstly, hot runner injection molding eliminates the need for runners and sprues, resulting in reduced material waste and lower production costs. This not only leads to cost savings but also promotes environmental sustainability. Secondly, hot runner systems provide precise temperature control throughout the molding process. This ensures consistent and uniform part quality, reducing the occurrence of defects such as warping, sink marks, or uneven filling. The ability to maintain optimal temperature also improves the flow characteristics of the molten plastic, resulting in enhanced part aesthetics and dimensional accuracy. Moreover, hot runner injection molding offers greater design flexibility. The elimination of runners allows for the production of more complex and intricate part geometries, enabling the creation of highly customized and intricate components. This versatility opens up new possibilities for product innovation and differentiation. Additionally, hot runner molds enable faster cycle times compared to traditional cold runner molds. This increased efficiency translates into higher productivity and shorter lead times, enabling our customers to bring their products to market faster. Overall, our hot runner injection molding molds provide numerous advantages, including reduced material waste, lower production costs, improved part quality, enhanced design flexibility, and faster cycle times. These benefits make our molds an excellent choice for customers seeking high-quality, cost-effective, and innovative solutions. |
Display diagram